Forklift GPS Tracking Benefits
In the fast-paced world of warehousing, manufacturing, and logistics, operational efficiency is everything. Forklifts are the backbone of material handling in these environments—moving goods, feeding production lines, and fulfilling orders with precision and speed. Yet despite their importance, forklifts often go under-managed, leading to preventable accidents, costly downtime, and operational inefficiencies that cut into a company’s bottom line.
That’s where forklift GPS tracking comes into play.
Once considered a high-end feature only available to major logistics firms, GPS tracking technology is now affordable and accessible for businesses of all sizes. Whether you operate a single distribution center or oversee a network of facilities, implementing GPS tracking for your forklift fleet can unlock a new level of visibility and control.
From real-time location monitoring to enhanced safety compliance, optimized forklift utilization, and cost-saving predictive maintenance, GPS tracking brings powerful insights into how your equipment is being used—and misused. It empowers warehouse managers to make data-driven decisions that improve workflow, protect workers, reduce operating costs, and boost ROI.
In fact, companies that adopt forklift tracking often discover inefficiencies they never knew existed. Whether it’s excessive idle time, overlapping routes, unauthorized usage, or poorly maintained equipment, GPS tracking shines a light on hidden issues and provides the tools to fix them.
This article explores the full spectrum of forklift GPS tracking benefits, including how it improves warehouse safety, enhances fleet visibility, optimizes utilization, and reduces costs. We’ll also highlight real-world case studies, key features to look for in a system, and emerging technologies that are shaping the future of forklift operations.
If you’re looking for ways to improve productivity, reduce liability, and stay competitive in a data-driven world, now is the time to consider GPS tracking for your forklift fleet.

Real-Time Forklift Monitoring
Real-time forklift tracking gives managers a live view of each forklift’s location, movement, status, and task. This transparency enables more efficient operations by preventing overlap, reducing delays, and ensuring high-priority tasks receive immediate attention.
For example, during a high-volume shipping period, a warehouse manager can see that two forklifts are idle in a distant aisle and immediately reassign them to loading docks experiencing a bottleneck. Without GPS tracking, this level of responsiveness is impossible.
Integration with Warehouse Automation
In automated or semi-automated environments, GPS tracking can be integrated with robotics, conveyor belts, and warehouse management systems (WMS). This synergy allows systems to dynamically assign tasks based on equipment location, reducing decision lag.
Dashboards That Drive Action
Leading GPS platforms offer cloud-based dashboards with filters for shift, asset type, or location. These dashboards often include heat maps that show traffic patterns, revealing congested areas that may benefit from reconfiguration.
Industry Example
In the cold storage industry, tracking is especially vital. With temperature-sensitive goods, managers use real-time data to ensure forklifts move quickly between refrigeration units and shipping docks, preventing spoilage.
Improve Warehouse Safety
Statistics and Safety Mandates
Forklifts are involved in nearly 85 fatalities and over 7,000 serious injuries annually in the U.S., according to OSHA. Most of these incidents stem from speeding, poor visibility, or unauthorized use. GPS tracking addresses these root causes by enabling behavioral oversight and access control.
Monitor Operator Behavior
Systems equipped with accelerometers and gyroscopes can detect:
- Harsh braking
- Sharp turns
- Collisions
- Speeding
Operators are notified in real-time, while managers receive daily or weekly safety reports.
Enhance Training & Accountability
With accurate operator performance data, training programs can be tailored to correct specific behaviors. Some companies gamify safety, offering rewards to drivers who complete their shifts with top scores in safety metrics.
For instance, a manufacturing plant in Indiana reported a 40% reduction in safety violations after launching a driver scoring program powered by GPS analytics.
Control Access with Operator ID
Modern GPS systems support RFID badge integration, ensuring only certified personnel can operate forklifts. This not only reduces unauthorized use but also helps comply with OSHA’s requirement that operators be trained and evaluated every three years2.
Investigate Incidents Efficiently
In the event of an accident or equipment failure, GPS data provides a forensic timeline, including speed, location, impact forces, and duration of use. This log supports insurance claims, compliance reviews, and internal root cause analysis.
Optimize Forklift Utilization
Understand Usage Patterns
Underutilized forklifts tie up capital and increase maintenance costs. GPS tracking enables usage reports that highlight:
- Daily hours of operation
- Frequency of idle time
- Time spent traveling vs. lifting
- Repeated routes and wasted movement
Utilization Benchmarks
Industry benchmarks suggest forklifts should be utilized at 65–75% of available time during operating hours. A fleet operating below 50% may have more forklifts than needed—or mismanaged deployment.
Layout Optimization
GPS heat maps help identify inefficient traffic flows, allowing businesses to redesign aisles, racks, or storage locations. For example, repositioning high-turn inventory closer to shipping docks can cut travel time by 25%, increasing daily task capacity.
Adapt to Seasonality
Companies with seasonal spikes—such as food distributors during holidays—use GPS data to allocate more forklifts and operators during peak weeks, avoiding overtime and overworking assets.
Predictive Maintenance Scheduling
Beyond usage tracking, telematics-enabled GPS units monitor:
- Engine hours
- Hydraulic pressure
- Battery charge cycles
- Tire wear
This data helps plan preventive maintenance based on actual wear rather than time-based intervals, minimizing unplanned downtime. According to McKinsey, predictive maintenance can reduce breakdowns by up to 50% and lower maintenance costs by up to 40%.
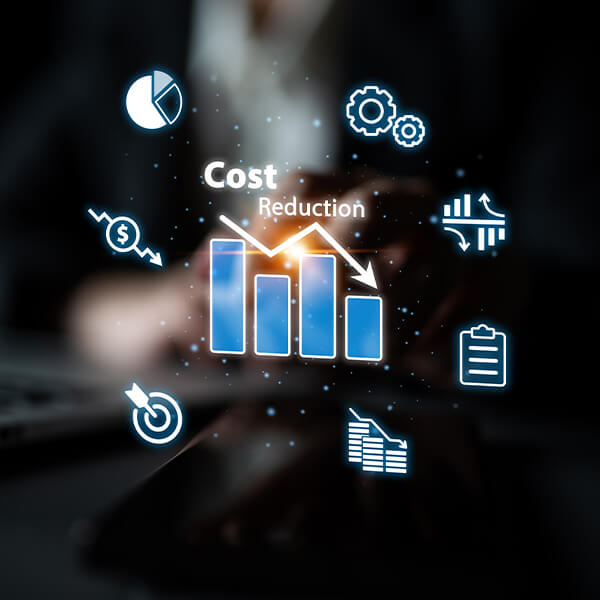
Reduce Operational Costs
Forklift GPS tracking drives cost savings in several areas, including energy consumption, labor, insurance, and theft prevention
Cut Fuel and Energy Waste
Tracking software identifies excessive idling, long travel paths, and redundant trips. By rerouting and enforcing idle alerts, companies have seen a:
- 20% drop in diesel consumption for propane-powered forklifts
- 15% increase in battery lifespan for electric models
In warehouses running 24/7, even small reductions in wasted movement lead to massive savings over time.
Insurance Discounts and Risk Mitigation
Many insurers offer premium discounts (typically 5–15%) for GPS-equipped fleets. Why?
- Real-time data reduces fraudulent claims
- Risk behavior can be proactively managed
- Location tracking aids in faster claims investigation
Prevent Equipment Theft
A stolen forklift can cost $20,000 to $50,000 in replacement value, not including lost productivity. GPS systems with geo-fencing send instant alerts when equipment exits approved zones. Some even allow for remote engine disablement.
A construction supply distributor in Texas recovered two stolen forklifts within 24 hours thanks to real-time GPS alerts.
Labor Efficiency
With real-time tracking, managers can reassign workers on the fly and reduce delays. Companies also report improved shift planning, as data shows exactly how many operators are needed per task cycle.
In one case, a food distributor reduced its forklift labor costs by 12% after matching staffing levels to GPS-documented demand trends.
Enhance Fleet Visibility
Fleet visibility is more than just knowing where assets are—it’s about understanding how they’re used, by whom, when, and why.
Unified Management Across Locations
Multi-site operators can monitor forklifts at all locations from a single dashboard. This reduces the need for on-site supervisors and enables standardized safety and performance KPIs.
A Canadian retailer managing 10 regional warehouses unified all forklift tracking into one central platform, cutting fleet management time by 35%.
Real-World Case Studies
Case Study 1: National Retailer
A major U.S. retail chain implemented GPS tracking across 100+ forklifts in its national distribution centers. Within six months:
- Order fulfillment time decreased by 30%
- Idle time per forklift dropped by 18%
- Safety incidents involving collisions dropped by 40%
The company used heat maps to redesign aisle traffic, resulting in fewer congestion points during peak hours.
Case Study 2: Beverage Logistics Company
A regional beverage distributor in Florida integrated forklift GPS tracking with its ERP. It used the data to:
- Eliminate 2 unused forklifts from its fleet
- Lower annual maintenance costs by $28,000
- Achieve a 12% drop in insurance premiums
- Cut fuel use by 17% through route optimization
Final Thoughts
As warehouses and industrial operations evolve to meet the demands of modern supply chains, forklift GPS tracking has emerged as a cornerstone technology for smarter, safer, and more efficient facilities. It’s no longer enough to manage forklifts reactively—today’s leaders are turning to data-driven strategies that give them proactive control over equipment, labor, and logistics flow.
By investing in GPS tracking, businesses gain the ability to see everything—from how long a forklift sits idle, to where safety risks are emerging, to which assets are underused or overworked. This kind of transparency not only improves day-to-day operations, but also supports broader business goals like lowering insurance costs, improving customer service levels, and meeting sustainability benchmarks.
Forklift tracking also plays a vital role in risk management. With OSHA regulations tightening and workplace safety under increasing scrutiny, the ability to log, report, and analyze forklift behavior is a game-changer. Companies can reduce injuries, prevent costly downtime, and avoid fines—while simultaneously improving employee morale by creating a safer and more organized work environment.
On the financial side, GPS tracking helps optimize fleet size, cut unnecessary fuel or energy costs, and extend the lifespan of high-value equipment. With predictive maintenance and data-driven usage insights, businesses can reduce repair bills and avoid emergency part replacements. Over time, these efficiencies can translate into hundreds of thousands of dollars in savings.
But perhaps the most important benefit is agility. In an unpredictable market—where consumer demands shift rapidly and labor shortages persist—GPS tracking gives managers the real-time intelligence they need to adapt, scale, and innovate faster than the competition.
Whether you’re looking to improve forklift safety, reduce costs, enhance efficiency, or prepare your facility for the future of logistics, GPS tracking offers a smart, scalable solution. The technology is mature, the ROI is proven, and the competitive advantages are significant.
In short, GPS tracking isn’t just about monitoring—it’s about mastering your warehouse operations.
Now is the time to transform your forklift fleet into a strategic asset. With the right GPS tracking solution in place, you’ll gain the visibility and control to take your operation to the next level—safely, efficiently, and profitably. Contact us today and learn more about our Forklift GPS Tracking Benefits at GPS Leaders.